Prevent Ink on Delicate Substrates
How to prevent ink on delicate substrates from overheating with the Exergen IRt/c.03
MHM is an innovative screen-printing equipment company. It was founded in Erl, Austria in 1980. MHM has been a pioneer in the textile screen printing machines segment representing innovation, quality, and reliability. Design and manufacturing take place in Austria.
Flash Curing Machines
MHM offers the latest innovations in screen printing equipment by providing quality and efficiency in a cost-effective manner. One of the products MHM develops and manufacture are Flash Cure Units. These units are used for curing (i.e., drying) the screen-printed t-shirts. This flash cure line excels in versatility.
Challenge
Efficiency requires radiant lamps and/or more densely packed lamps causing high temperatures of 1200°C to 1600°C (2192°F to 2912°F). MHM has its dryers equipped with two different lamps. These are the MW (medium wave/carbon) or HTL lamps (Halogen Tungsten Lamps). The most important differences between MW and HTL lamps are the drying time and temperature. The MW lamp goes to 1200°C (2192°F) and the HTL lamp to 1600°C (2912°F). First one is much more economical. The choice between the MW and HTL lamps can therefore be made more thoughtfully by a company.
The lamps cause a main problem:
The challenge for MHM is to increase efficiency for curing the screen-printed t-shirts, keeping a high-quality print by ensuring that the ink on delicate substrates can’t overheat. If this happens it will surely damage the garment resulting in additional waste and therefore increased costs. But the largest problem could be a possible brand problem. Companies like Nike and Adidas work with extremely high standards and only work with state-of-the-art partners.
The solution for MHM has been found in the use of an unpowered IRt/c.03 sensor of Exergen. The teams of MHM and Exergen were able to tackle the problems by working closely together. MHM and Exergen Global selected the IRt/c.03 sensor for optimal performance. The 3:1 field of view allows for positioning of the sensor behind the IR lamps. In this way the sensor is protected from direct heat from the IR lamps. The IR sensor is cooled by continuous airflow to further prevent overheating. In between the IR lamps, the sensor has a clear view of the printed T-shirts and measures the T-shirts accurately and quickly. By measuring the dry-out point, the IR sensors can be used to reliably measure when a printed surface is sufficiently dried. This enables the operator to optimize the speed of drying, and thus the speed of T-shirt printing without jeopardizing the print quality.
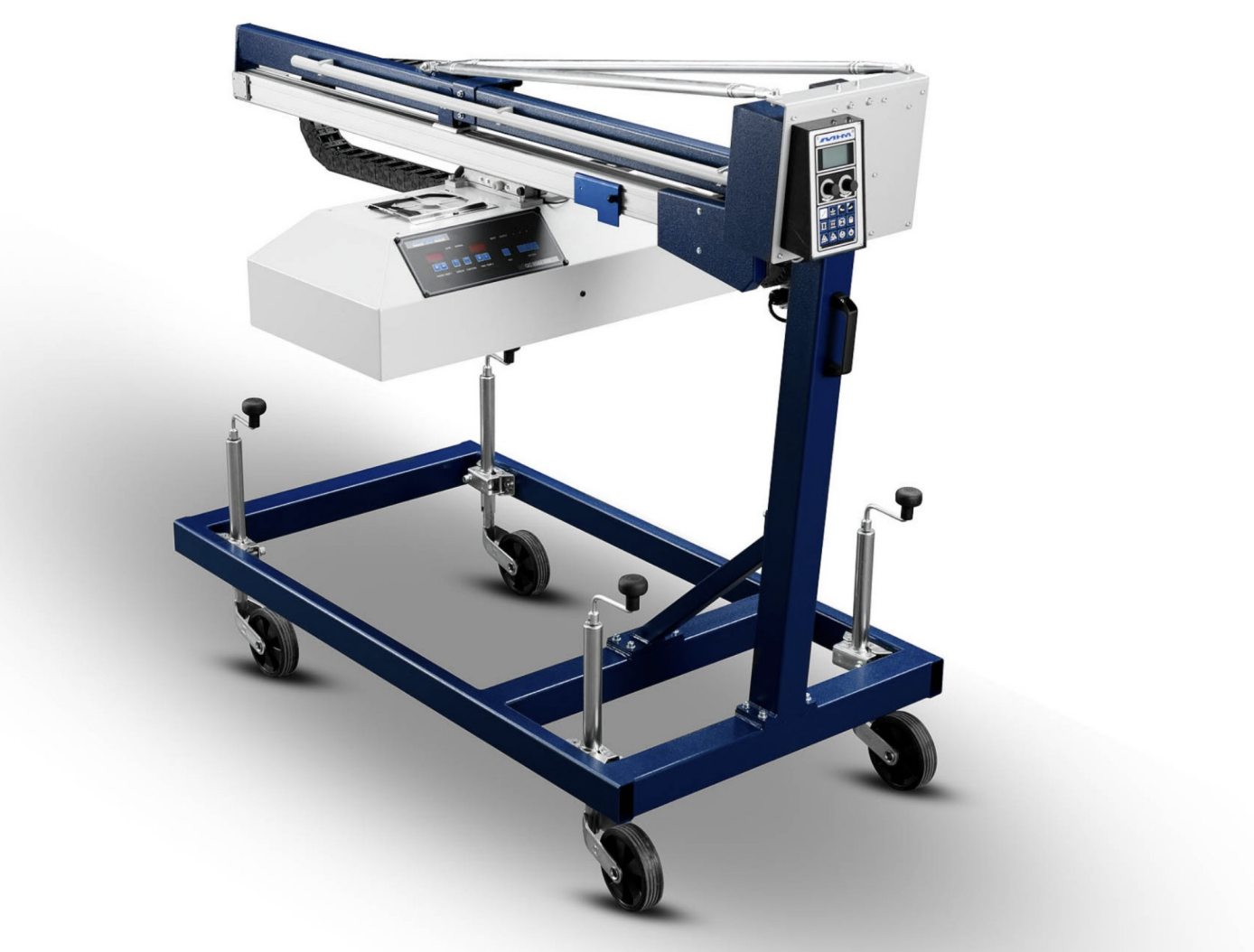
Benefits
The IRt/c sensor from Exergen Global makes it possible to measure the exact t-shirt temperature during the curing process, by employing sensors with a resolution of approx. 0,0001°C (0.0002°F) and a repeatability error of 0,01°C (0.02°F). Once the customer implements the parameters of material of textile, color and ink, the optimal curing temperature will be known, and the sensor will indicate when it overheats. This ensures that MHM knows exactly when to remove the t-shirt. Because of the solutions that the teams of MHM and Exergen brought, MHM can increase the intensity of the radiant lamps, which produce more heat. Doing this and being able to control it, MHM increases the efficiency of the process whilst prohibiting that the ink on delicate substrates overheat. Next to this, on average, there is a gain of approx. 2 seconds providing a speedier printing process.