Sensoranics
This is a unique methodology developed by CleverIR to augment the performance of our non-contact IR sensor technology using the smart mechanics approach that is the hallmark of CleverIR’s competitive difference combined with implementing in depth knowledge of thermal management processes.
Sensoranics requires three building blocks.
1. Innovative sensor technology is the basis for the Sensoranics approach, and our non-contact IR sensors that measure temperature, are the foundational building blocks. The working of a sensor can be compared with a human eye: it converts electromagnetic radiation into an electrical signal. Whereas the human eye sees visible light and colors, our sensor detects infrared radiation, which is a measure for temperature. The sensor can do this in a very accurate and reliable way because of its elegant design.
2. Adding mechanical features to sensor technology is the next ingredient for Sensoranics. Although the sensors are capable of reaching very high performance levels, they can be limited in doing so because of environmental constraints. The mechanical add-ons to the sensor are designed to remove the constraints. This is not a trivial task: the added mechanics can influence the trajectory of the IR waves, the surface properties of the used materials, and the thermal properties of the assembly. These must all be understood and accounted for to help increase the sensors performance. It is an approach that requires multidisciplinary knowledge.
3. A thorough understanding of thermal management. The sensor’s performance can only be augmented properly if there is an in-depth understanding of how IR waves interact with materials and surfaces, how heat is absorbed and reflected, how thermal energy is convected or conducted through materials, and how all these factors combined affect the sensor performance in its working environment. The term “working environment” is highlighted because the sensor’s environment has a profound impact on how it works. This must be understood in detail to provide a solution based on Sensoranics.
Measuring temperature accurately and reliably at process critical points is key to optimizing the application and increasing product throughput. As processes are getting faster and more technically advanced, it’s essential to have a more accurate temperature measurement. Similarly, environmental circumstances are becoming more challenging, pushing the limits of the sensors. Providing a solution that meet the very specific needs of application while addressing environmental challenges simply cannot be done with the one-product-fits-all approach. Off-the-shelve sensors will not provide the required reliability and accuracy.
Advantages
Sensoranics improves product quality by optimizing the production process based on the product’s actual temperature and thermal signature. It increases production throughput by using precise knowledge of actual temperatures and heat flows to increase application speeds,. These steps combine to increase a customer’s profitability, and decrease their costs (reduced energy consumption, less downtime and scrap). It's a very economic choice!
Our customers , especially in the graphics and medical/aestheitical market, are always looking for sensor solutions that offer better performance under more challenging circumstances. While other companies focus on a „one-product-fits-all” approach, CleverIR chooses to go after a very, very customized approach. Our sensor technology delivers very accurate and reliable measurements. However, as is true for all sensor technologies, some applications operate under strenuous conditions that make it difficult for the sensor to deliver maximum performance. For example, very high ambient temperatures or dusty environments can limit sensor performance. Sensoranics is aimed at reaching maximum sensor performance under the most challenging conditions. Think about a sports car with a lot of horse power: the car itself is capable of reaching high speeds, but it need additional equipment such as spoilers and special tires to allow it to reach those high speeds on a wet, curved track.
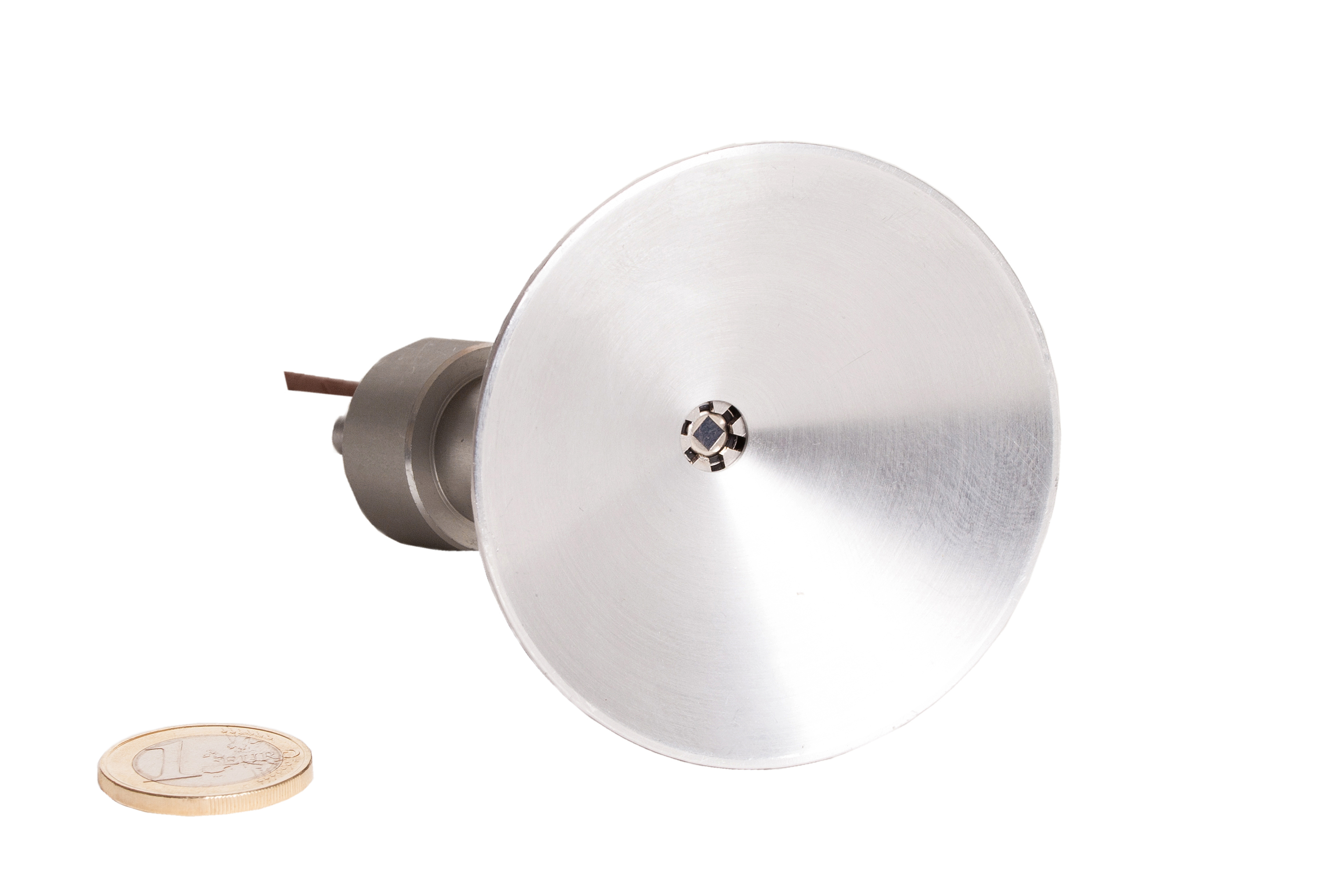
Cone
Customers frequently encounter challenges related to temperature control after they have designed sophisticated equipment specific to their production processes. The issues may be inherent in the materials used in production, the process itself, or another issue entirely – it differs in nearly every instance. By working closely with customers’ engineering teams, examining every step of the manufacturing process to understand where thermometry may come into play. By identifying that particular issue and then – in a combined effort - custom-design solutions to address the specific needs of the equipment, the application and the environment.
Many industrial applications require very accurate control of the production surface (e.g. the drum, blanket, silicon wafer or other) temperature to ensure high quality processing. Yet, during production, the emissivity of the surface – its power to emit heat relative to (ambient) radiation it reflects -- can vary considerably due to substrate properties, surrounding radiation, and ambient condition changes.Most conventional IR thermometry devices do not account for those frequent and sometimes significant changes in surface emissivity, resulting in less accurate temperature readings. Exergen’s Cone overcomes this problem because its custom-fitted conical design prevents ambient radiation from entering the surface being measured, and reflects emitted radiation and directs it to the sensor detector. By decreasing ambient reflections and emissivity variations, the Cone reduces temperature measurement errors by about a factor of ten.
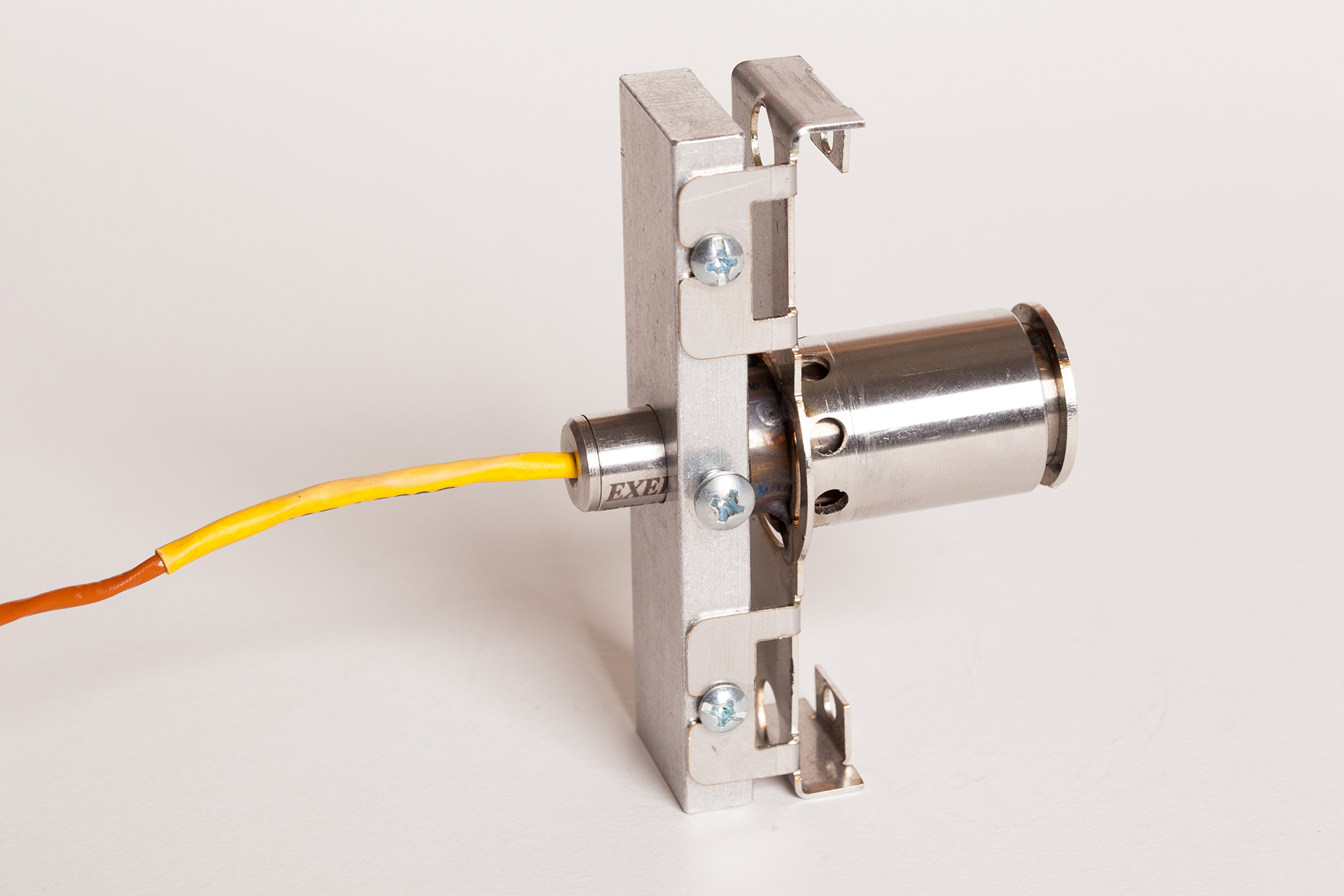
M&R Sensor
Solution
The solution for M&R’s RED CHILI D and their CAYENNE D. has been found in the use of a completely customized IRt/c sensor. The teams of M&R and Exergen were able to tackle the problems by working closely together.The first problem, overheating the sensor during operation has been solved in a simple, cost effective manner. Using a baffle system, more air will be directed from the fan to the sensor area. This causes the temperature to drop to 70°C. To prevent overheating of the sensor after shutting down the power a fan will be turned on to cool the sensor. But in case that all power is shut down by storm or an accident, they came with an other solution. They clamped a simple aluminum heat sink of sufficient mass to the sensor to absorb the conducted energy without raising the temperature of the sensor excessively.The last challenge has been solved by shrouding the field of view of the sensor. The shroud becomes part of the optical system for the sensor as well as preventing any direct lamp energy from entering the sensor. The wider field of view is effectively funneled by the reflecting shroud, making a wide area measurement, which is more desirable from a quality control perspective. Besides shrouding the field of view of the sensor, the double walled shroud insulate the inner surface from the intense heat of the lamp.
Benefits
The IRt/c sensor from Exergen Global makes it possible to measure the exact t-shirt temperature during the curing process, with a resolution approx. of 0.0001°C and a repeatability error of 0.01°C.This ensures that M&R knows exactly when to remove the t-shirt. Because of the solutions that the teams of M&R and Exergen brought, M&R is able to increase the intensity radiant lamps, which produce more heat. Doing this and being able to control it, M&R can increase the speed of the curing process.
